CNT fiber
Multi-scale experiments and interfacial modeling of CNT fiber
Topic A: Deformation mechanism of CNT fiber
Carbon nanotube (CNT) fibers exhibit high mechanical properties and possess good thermal and electrical conductivity that indicate potential as multi-functional materials. Studying the strengthening and toughening mechanisms of CNT fibers is critical to the future applications of fibers and fiber-based composites.
The CNT fibers used for this study were prepared from the chemical vapor deposition (CVD) aerogel process, with diameters typically in the range of 130–150 μm. The mesoscopic structure of the fiber consists of relatively thick, straight bundles and fine, curly threads preferentially aligned along the fiber axis. The bundles and threads have diameters ranging from 30 to 100 nm. Transmission electron microscopy (TEM) images show the microscale structure of the fiber. The CNTs within bundles (threads) are double-walled and their diameters are approximately 8 to 10 nm. Owing to their large diameters, these double-walled nanotubes (DWNTs) appear flattened with a “dog-bone” cross-section. At the nanotube level, the microscopic structure is composed of flattened DWNTs that are closely stacked into bundles and threads, similar to graphitic layer stacks. Therefore, interfacial contact and load transfer in the fiber occur between both the mesoscopic bundles/threads and the microscopic nanotubes. We investigated the multi-scale deformation and interfacial mechanical behavior of CNT fibers with multi-level structures via experimental and theoretical methods.
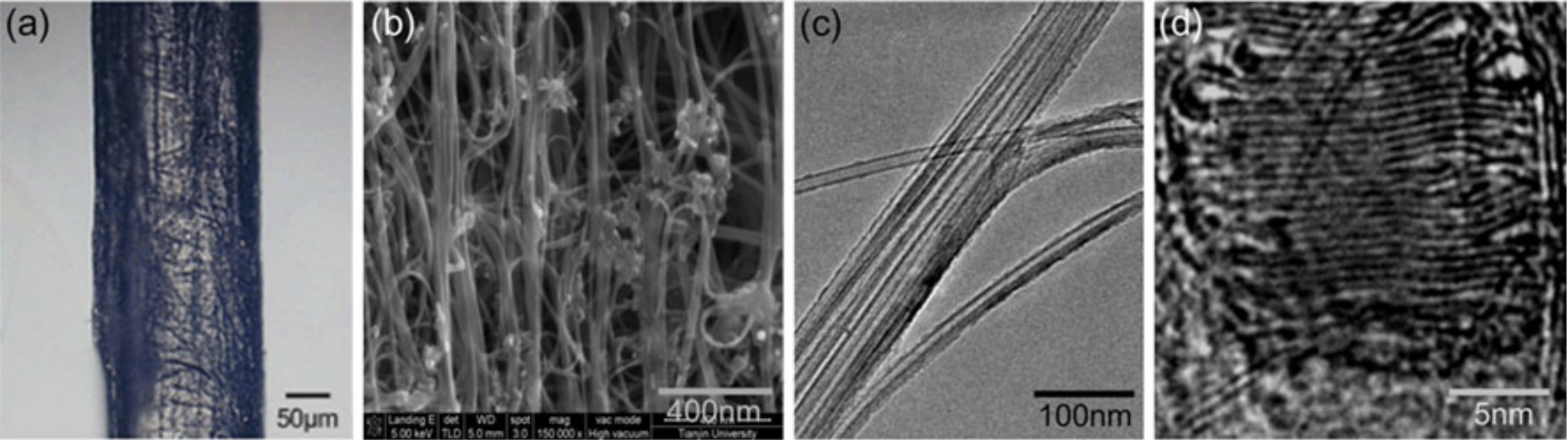
Multi-scale experiments including uniaxial tensile testing, in situ Raman spectroscopy, and scanning electron microscopy were conducted to measure the mechanical response of multi-level structures within the fiber under tension.
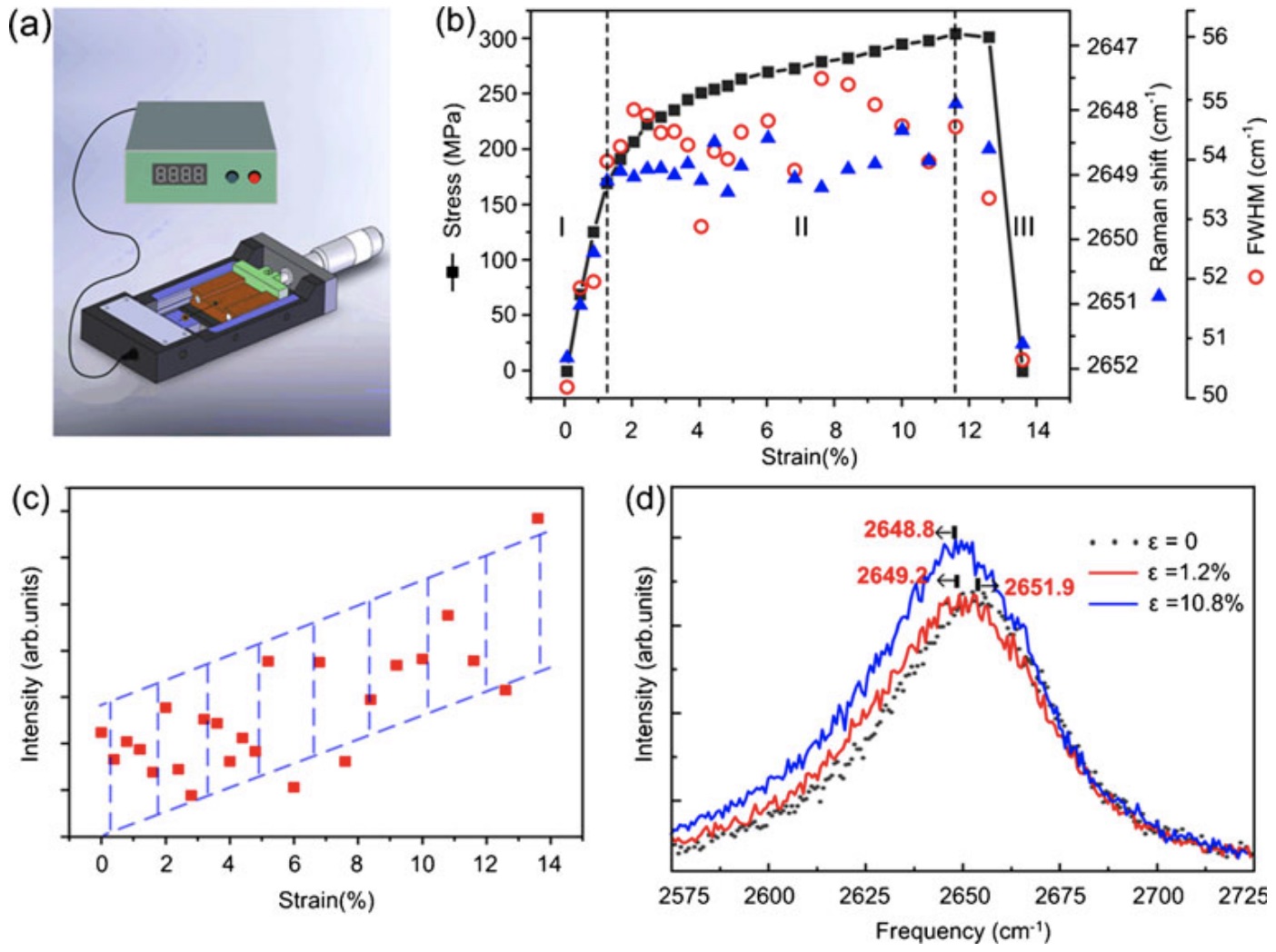
A two-level interfacial mechanical model was then presented to analyze the interfacial bonding strength of mesoscopic bundles and microscopic nanotubes. The analysis suggests that the mesoscopic interface between bundles is weaker than the microscopic interface between DWNTs. Therefore, the weaker interface in the fiber is identified and slipping beyond a critical load will first occur at the inter-bundle interfaces.
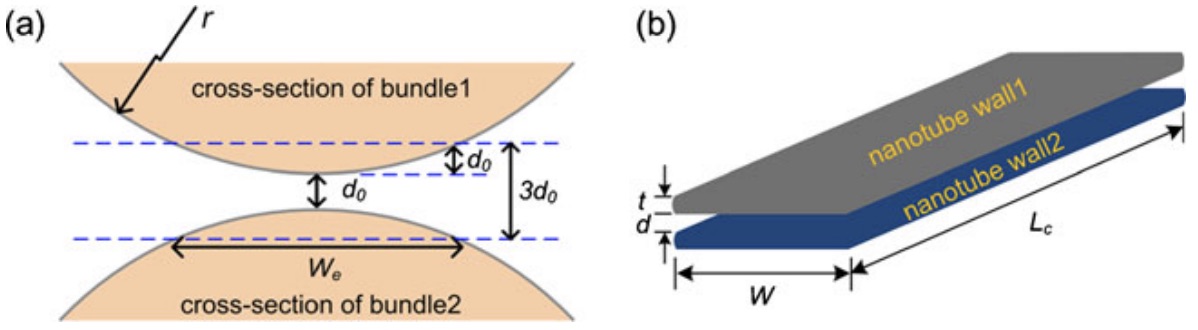
The evolution characteristics of multi-scale deformation of the fiber were described based on experimental characterization and interfacial strength analysis. Comprehensive analysis showed that the property of multi-level interfaces is a critical factor for the fiber strength and toughness. The result can be used to guide multi-level interface engineering of CNT fibers and fiber-based composites to produce high performance materials.
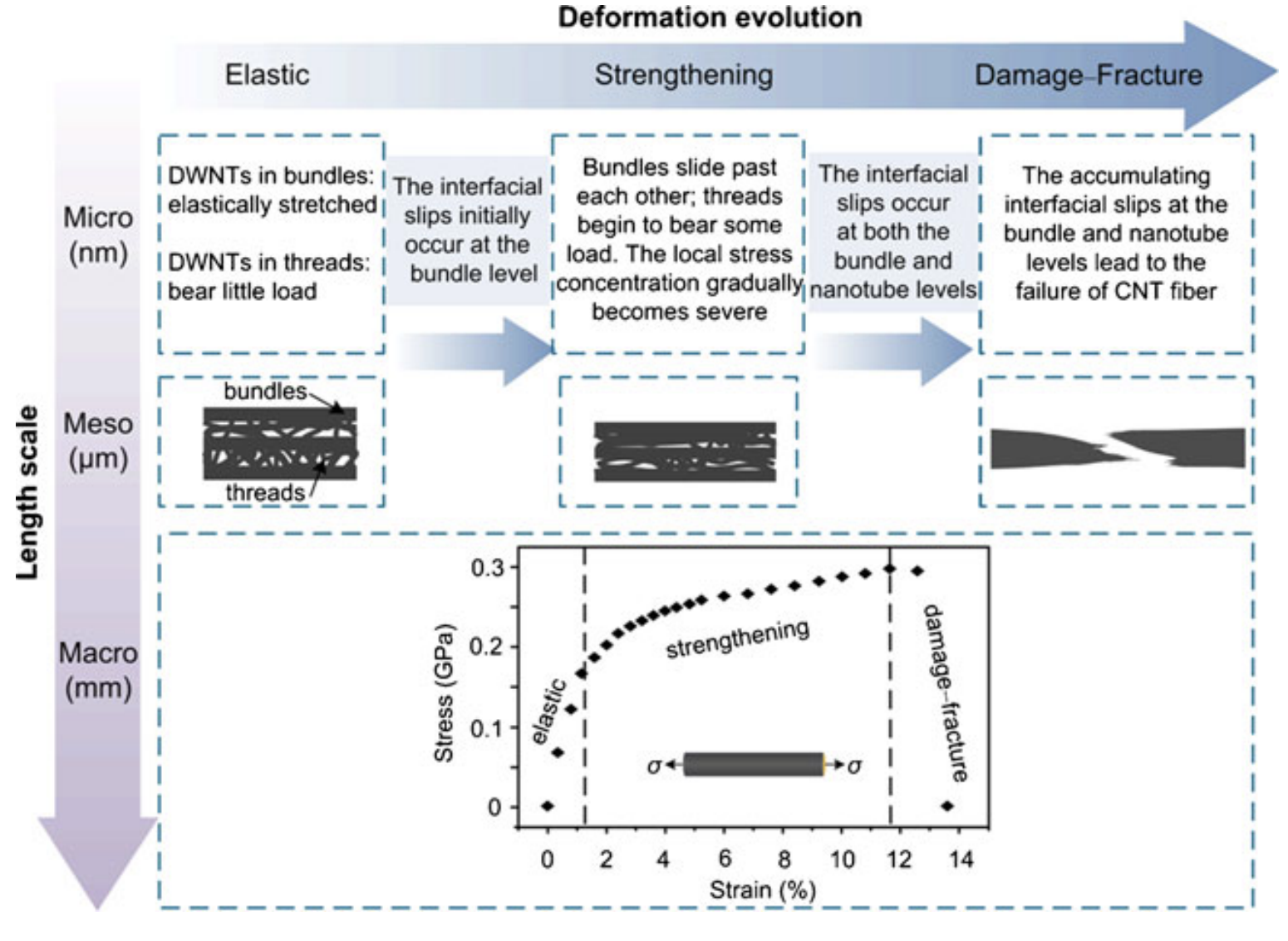